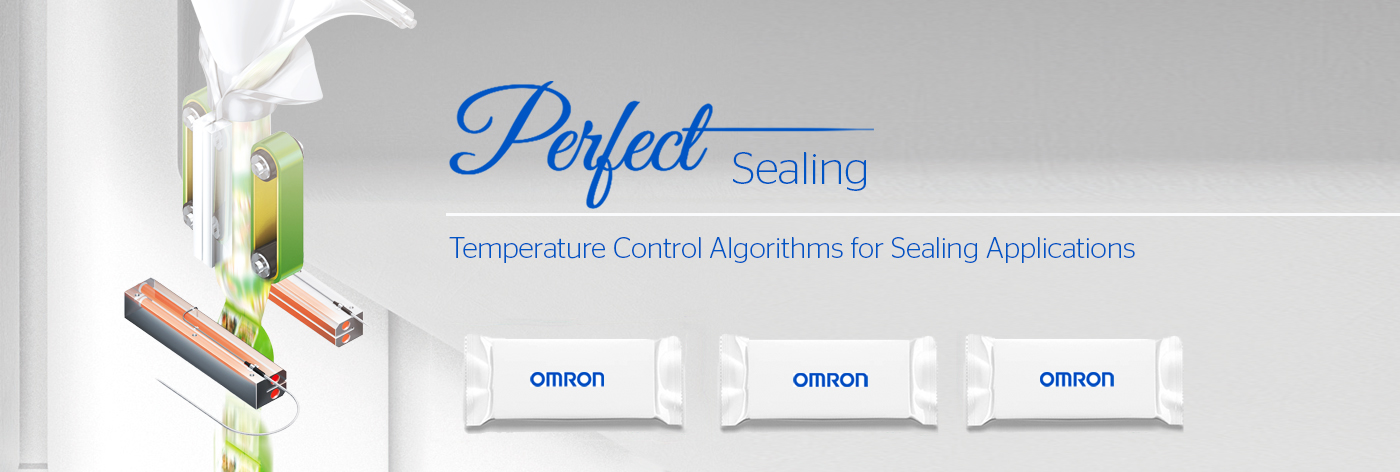
Perfect Sealing
When it comes to packing, we all have one goal, and that is to attain the best way to move vulnerable goods from the producer to the consumer. Extending the shelf life and protecting the product is the main essence of packaging. Who doesn’t want the product to reach its consumer in a perfect state?
However, as consumers become more aware and educated, companies are now ecologically challenged than before. Regulatory demands for thinner packaging materials, reduction of waste and longer shelf-life are pressures packaging companies face these days.
With increasing number of consumers and the perpetual target to reduce costs, the need for higher output is obvious. The balance between quantity and quality is now more apparent – faster machines to achieve higher output with better quality sealings right from the first pack.
Challenges
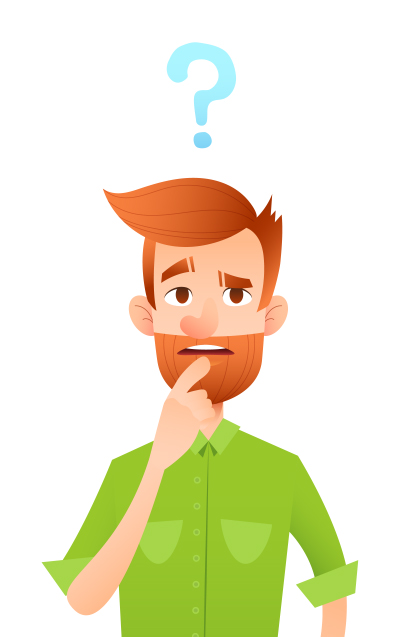
1.
Traditionally, temperature sensors are often located far away from the sealing surface of the heating bar. This causes a difference between the temperature of the sealing surface and the temperature that was being controlled.
2.
When moving from the idle stage to production stage, the balance in the Proportional, Integral, Derivative (PID) control loop is heavily disturbed. The big drop in temperature at start-up results often in many bad packages.
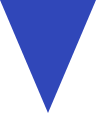
Solution
1.
OMRON’s sensors can be placed close to the sealing surface to acquire the correct measurement. Omron’s AI Temperature Algorithm helps control the disturbance level from the heating bar.
2.
Once operator gives the signal for the machines to start, we can prepare the seal-jaw temperature for the soon-coming-drop and pre-compensate for that. The technology Omron is using to achieve this is called Direct Power Control (DPC). It provides heating output feed forward control in conjunction with Omron’s unique 2-PID temperature algorithm AND is in-sync with the motion of the machine.
This helps to increase production by keeping the temperature consistence even when the machine stops. Hence, contributing towards a balance between quantity and quality.
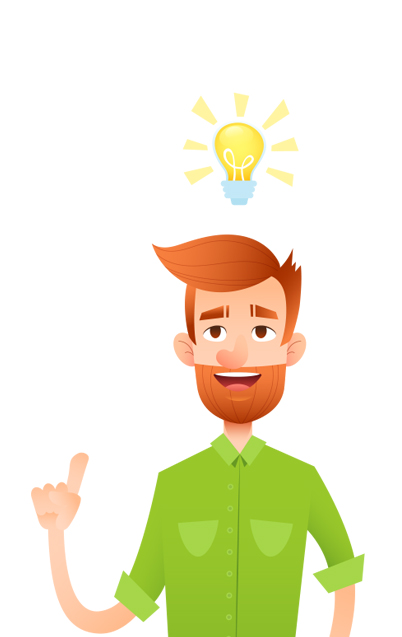
Benefits
Ideal for thin packaging materials.

Minimise
Scrape
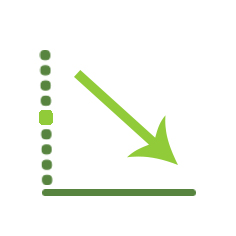
Fast Film Change-overs
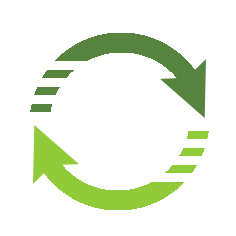
Increase Food Lifespan
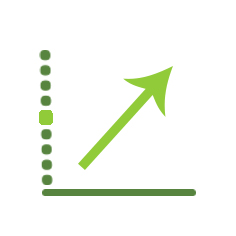
Thinner packaging materials
Thinner packaging material requires an exact temperature at a given pressure to ensure a good seal.
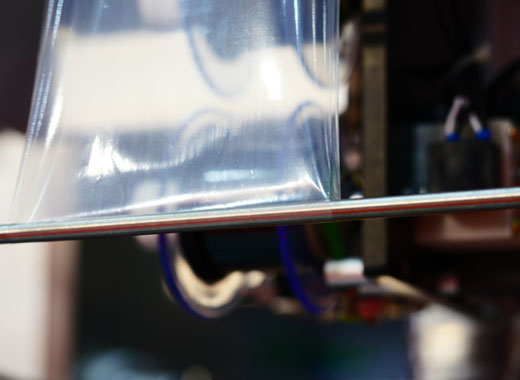
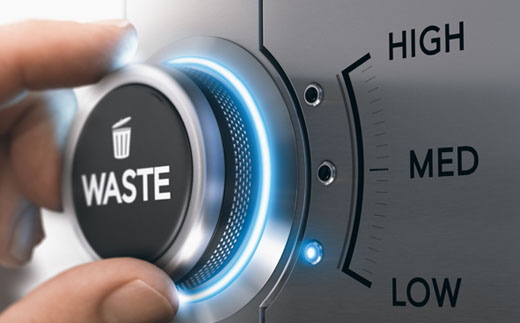
Minimise Scrap
With sensors placement near the heating bar, the sealing temperature is controlled to the exact amount needed for a good seal.
Fast Change-Over
Change of film requires adjustment of temperature parameters, usefully performed by a skilled operator. System with Artificial Intelligence algorithms automatically adjusts.
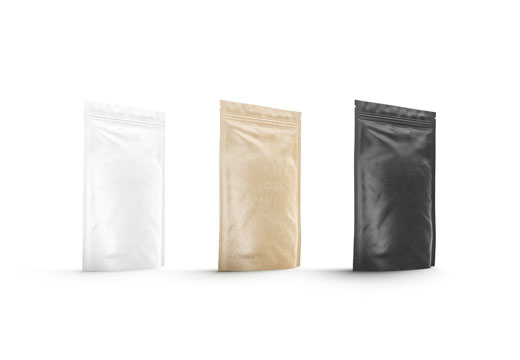
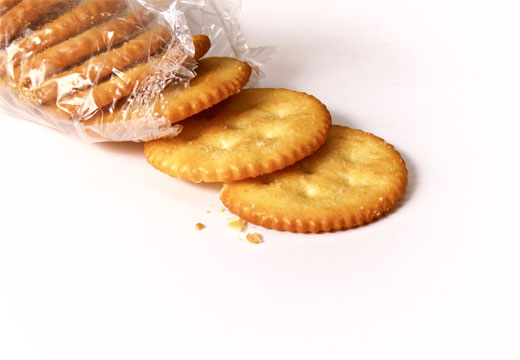
Increase Product Lifespan
The sealing of the packaging helps to keep the product fresh for a longer period of time. With a tight seal it is hard for mold, mildew, or microbes to spoil the product. Better quality sealing right from the first pack you produce is fundamental to extend the lifespan of the food.
Products
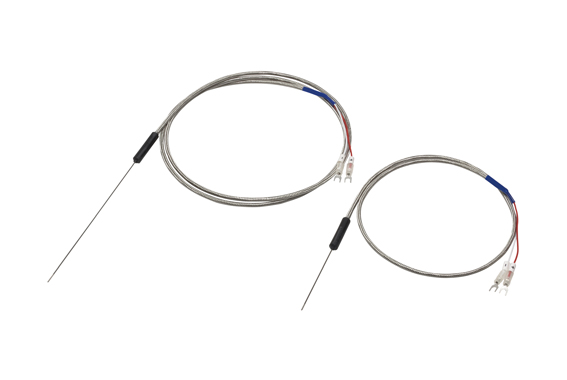
E52 (For packaging machine)
Temperature sensors for advanced applications.
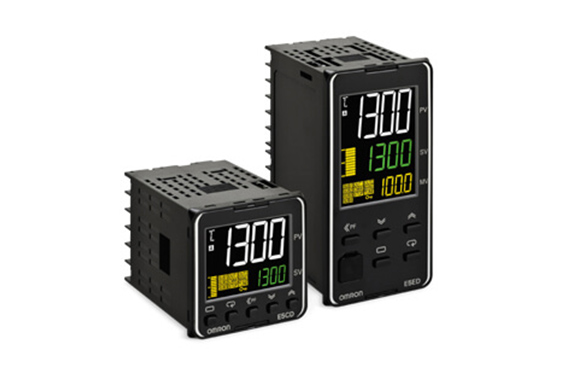
E5_D
Next generations of controllers.
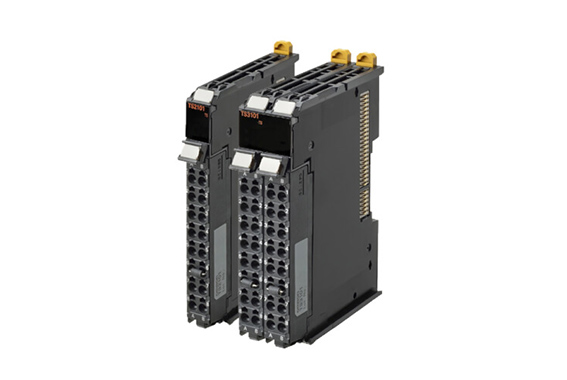
NX-TC
Next generations of controllers.
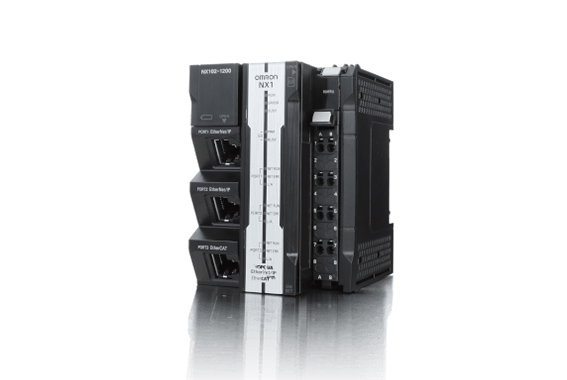
NX1
Information and Productivity in a miniaturized size controller.
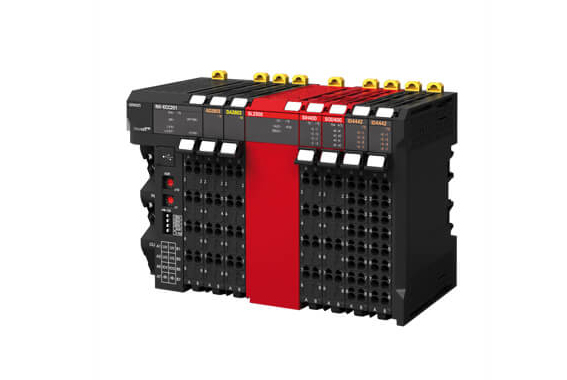
NX Series
Performance and practicality for machine control.

NX7
Sysmac controller.

NJ1
Sysmac controller.
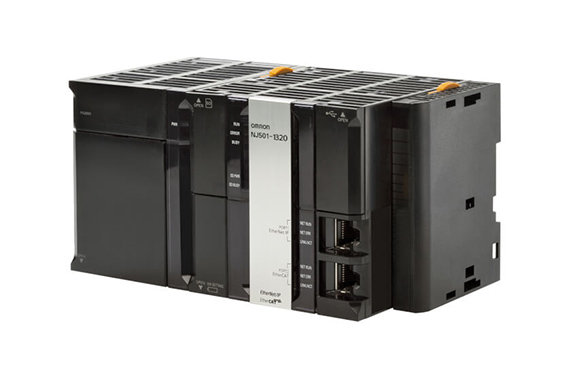
NJ5
Sysmac controller.
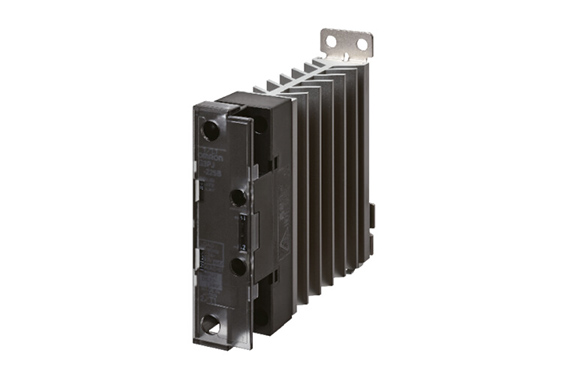
G3PJ
Solid state relays for heaters.
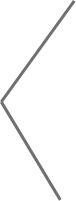
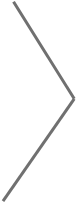