COMPONENT LEVEL
SUBASSEMBLY LEVEL
MAJOR ASSEMBLY LEVEL
FINAL ASSEMBLY AND SHIPMENT LEVEL
A reliable traceability system fortifies the supply chain right from the start of production. Should a faulty part be detected further along the production line it will be easier to pinpoint the source of the problem and quickly rectify the situation.
Crucial information for product tracking like serial numbers, place of origin, model number and source manufacturer can be encapsulated into a barcode affixed to a part. To ensure each part carries this data along the supply chain, this barcode is usually a direct part mark (DPM) – a marking that is etched or printed directly to ensure it is permanent and inseparable from the part itself. Manufacturers can also facilitate traceability by using labels.
Crucial information for product tracking like serial numbers, place of origin, model number and source manufacturer can be encapsulated into a barcode affixed to a part. To ensure each part carries this data along the supply chain, this barcode is usually a direct part mark (DPM) – a marking that is etched or printed directly to ensure it is permanent and inseparable from the part itself. Manufacturers can also facilitate traceability by using labels.
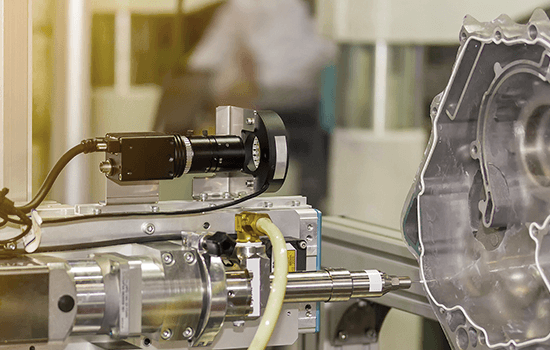
Immediate access to production history of each component is possible when the ERP or MES system integrates the data acquired from marking and reading codes.
This facilitates monitoring the assembly process and ensuring each task is meticulously executed. At the subassembly stage, the production history of all components added to the system is fully documented, enabling prompt response in the event of problems or issues that arise from a defective part early in the assembly process before it travels further along the supply chain.
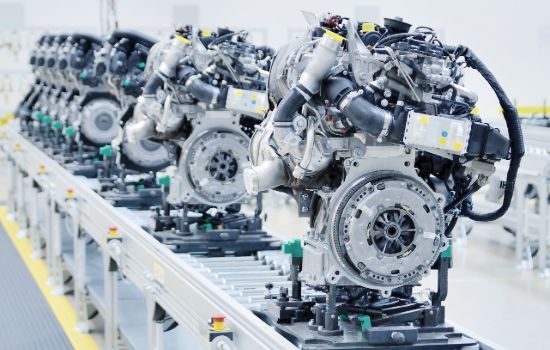
DPM identification will have greater benefits if utilised throughout the entire supply chain. It ensures exceptional precision in pinpointing the source of faulty parts or incorrect components further down the production line.
Final products that make it all the way to final quality control (QC) with incorrect components will need to be reworked resulting in substantial losses to productivity and high costs incurred. By then it is too late to trace the data of the incorrect component.
Manufacturers need robust traceability for regulatory compliance due to the sheer number of parts required for assembly at each of the 15-20 stages of the supply chain.
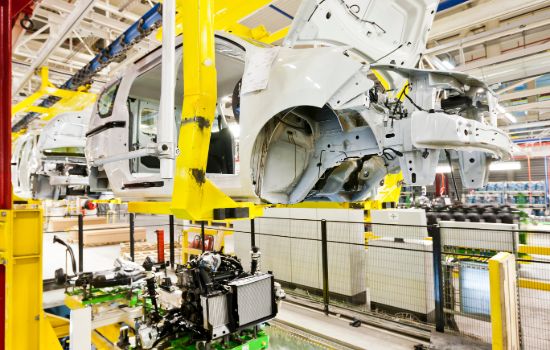
Operators can minimise errors by scanning each assembled component individually to accurately identify the major assemblies and subassemblies to be mounted. Each part number marked with important data such as quantity, customer name and destination of shipment can be accessed by scanning the final product.
A complete and robust traceability system essential for tracking of repairs and services issues further along the product lifecycle.
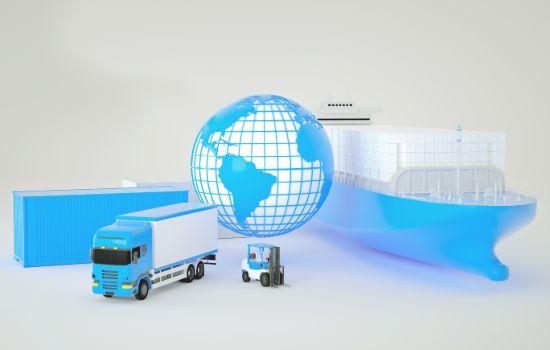
Omron offers one-stop solutions to implement “cradle to grave” traceability for Automotive Industry.
productsExplore automotive traceability solutions that ensure quality,
consistency and compliance.