STABLE DETECTION OF
COLOR MARKS ON GLOSSY PACKAGING

Aluminum vapor deposition prevents oxidation of glossy packaging. However, this process presents major
challenges for packaging machine manufacturers, especially for convention systems that are unable to
detect color marks on glossy packaging accurately in a consistent way. This increases maintenance effort
and packaging wastage.
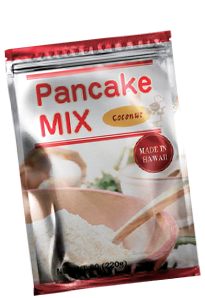
Highly-reflective glossy packaging
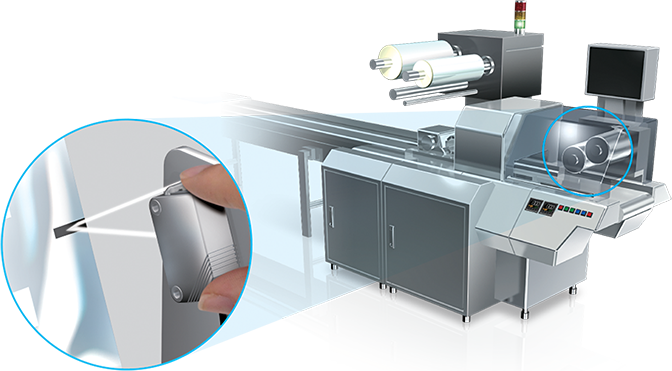
Detection of color mark on glossy packaging
Challenges Faced During
Color Mark Detection
1
In Figure 1, the light intensity received by the sensor from the glossy packaging is too strong. Therefore,
there is insufficient difference in incident levels to detect the color mark on the highly-reflective packaging.
(A situation known as saturation)
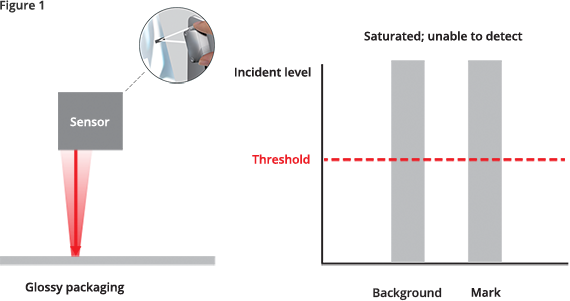
2
In Figure 2, the sensor is slightly tilted to avoid saturation, so as to detect the color mark on the packaging.
If the sensor is tilted too much, color mark detection will become unstable and inaccurate.
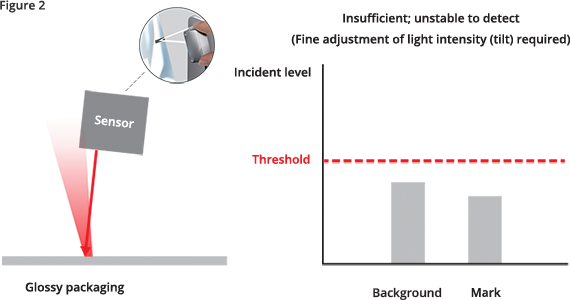
Color Mark
Photoelectric Sensor
(E3S-DC)
Wide Dynamic Range. No Saturation Occurs Even
With 99% Reflective Optical Mirrors
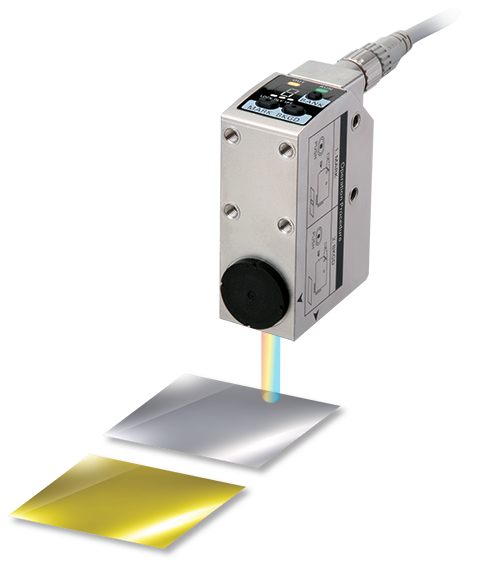
1
Wide Incident Light Range — No adjustment required
The high luminance RGB three-color LED light emitting element drastically improves the sensor's light intensity. Smart Noise Reduction technology is also applied to reduce noise. This results in a high dynamic range that prevents saturation when detecting glossy or mirror surfaces, without the need for adjustments.
The high luminance RGB three-color LED light emitting element drastically improves the sensor's light intensity. Smart Noise Reduction technology is also applied to reduce noise. This results in a high dynamic range that prevents saturation when detecting glossy or mirror surfaces, without the need for adjustments.
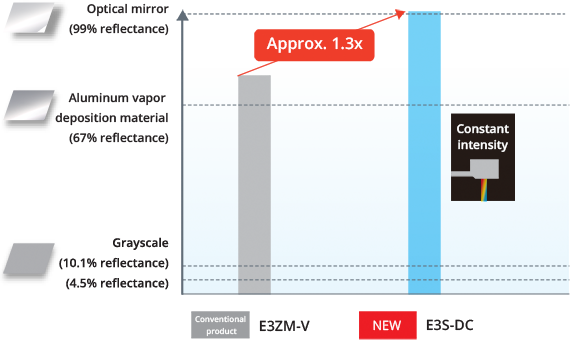
2
Stable Detection On Tilted Workpieces
Color mark detection on thin and soft wrapping paper can be difficult due to shifting angles. Equipped with OMRON's original narrow beam and a large optical system, stable detection is made possible with E3S-DC.
Color mark detection on thin and soft wrapping paper can be difficult due to shifting angles. Equipped with OMRON's original narrow beam and a large optical system, stable detection is made possible with E3S-DC.
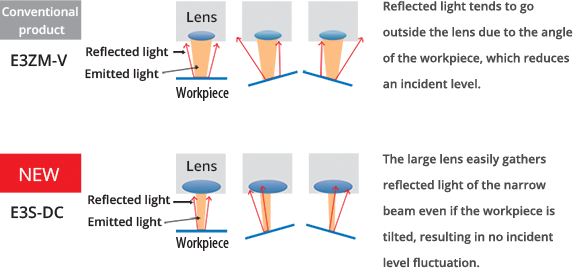
Color Fiber
Amplifier Unit
(E3NX-CA)
Wide Dynamic Range. No Saturation Occurs
Even With 99% Reflective Optical Mirrors
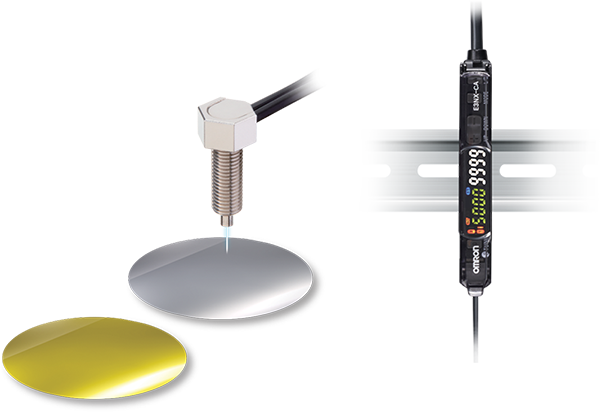
1
Easy Set-Up For Optimum Light Intensity
With high luminance white LED and Smart Noise Reduction technology, it significantly reduces noise and expands the light intensity adjustment range for the emitter and receiver to 1/100x and 1/3x respectively. This results in a high dynamic range that is four times that of conventional products. Optimum light intensity is achieved simply with 2 button presses on the amplifier unit.
With high luminance white LED and Smart Noise Reduction technology, it significantly reduces noise and expands the light intensity adjustment range for the emitter and receiver to 1/100x and 1/3x respectively. This results in a high dynamic range that is four times that of conventional products. Optimum light intensity is achieved simply with 2 button presses on the amplifier unit.
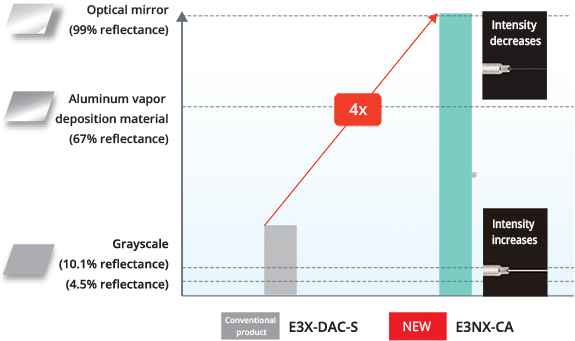
2
Stable Detection Even For Tilted Workpieces
Stable detection of color mark is made possible with OMRON’s E3NX-CA and coaxial Fiber Unit*, even on thin and soft packaging.
Stable detection of color mark is made possible with OMRON’s E3NX-CA and coaxial Fiber Unit*, even on thin and soft packaging.
*With an emission beam that covers 60° area, the Fiber Unit is capable of stable color mark detection even
of tilted glossy workpieces. It effectively receives diffusion light that carries color information, and does
not receive much of the specular reflected light.

Would you like to cut costly and painful downtime of locating faulty sensors in a large plant?
Download Our Brochure Get In Touch