Introducing OMRON Robust Components
Greatly Reduce Unexpected
Production Line Stoppages.
RESIST
OIL FOR
4 YEARS
Setting A New Oil Resistance Standard
OMRON Oil-Resistance Components Resist Oil for 4 Years
Five Products, more than 140 models available.
Splashing cutting oil on
conveyancing process
Robust compoents can be used
for the detection of cylinders
Robust limit switches used
for detection of drill breakage.
Robust compoents can be used
for the detection of cutting workpieces
OMRON Robust Components Deliver Breakthrough Value

As A Result, Company And Management Benefits From:
- Significant reduction in unexpected production line stoppages.
- Eliminate risks of lost opportunities resulting from downtime.
- Allow management to focus on new opportunities.
- Enjoy greater cost savings due to lower replacement frequencies of components - Only need to replace every 4 years, as compared to yearly corrosion and replacement of components.
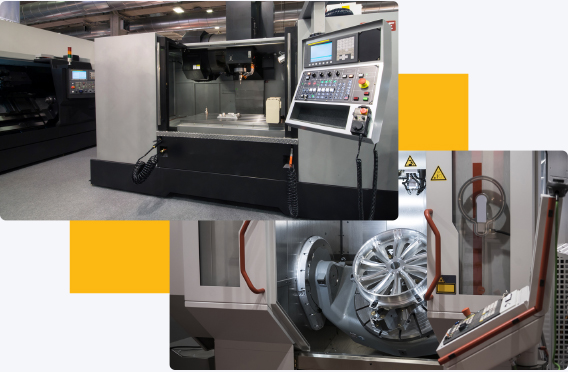
How Do We Achieve 4 Years Of Oil Resistance In Our Components
OMRON’s Oil-Resistant Component Evaluation Standards
OMRON’s oil-resistant components has been evaluated according to IP67G of JIS C 0920*2. We performed oil resistance testing with eight representative cutting oils that were used in manufacturing sites. Click to view
Based on our results, we are able to demonstrate and prove the competence of our product in achieving 4 Years Of Stable Operations In Resisting Oil.
OMRON Oil-Resistant Component Evaluation Standards | |
---|---|
Oil type | A1 (water-soluble cutting oil) |
Evaluation time | 2,000 hours of machining*3 800 hours of conveyance*4 |
Evaluation temperature | 55˚C |
Dilution concentration | Undiluted |
Criteria | Appearance, performance, and no labeling text loss |
Breakthrough Innovation In Oil Resistance (5 New Patents)
Patented Technologies To Resist Oil Ingress Into Your Components
Fluororesin Blocks Ingress From Cables
Fluororesin Sheath
Through analysis of the ingress paths of cutting oil, we determine that deterioration of cable sheaths is a large factor in causing component failure.
Henceforth, the cable sheaths of OMRON’s oil resistant components are made from fluororesin materials to provide maximum protection against the deterioration. This results in an impregnable cable to even highly aggressive cutting oils.
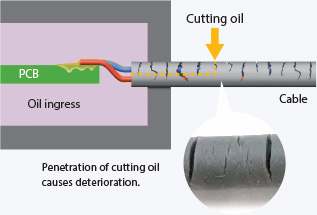
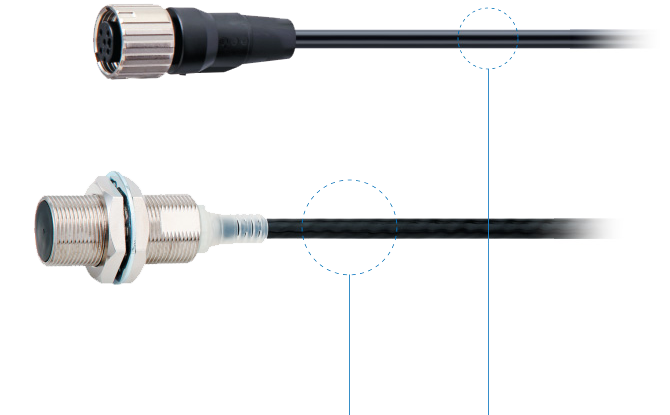
Connectors
XS5□R
Proximity Sensors
E2ER/E2ERZ
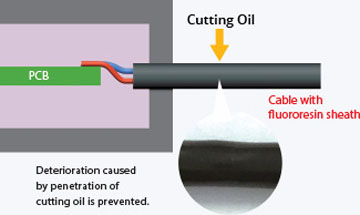
New Rubber Material Combining HNBR and Fluororubber
New Rubber Material
Limit Switches
D4ER-□N
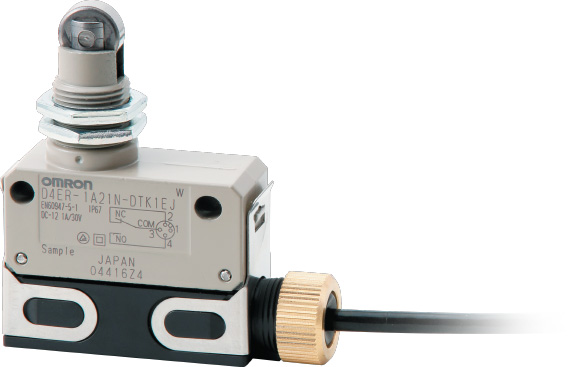
OMRON-developed Rubber Blocks Ingress Through Joints and Moving Sections
In addition to the deterioration of cable sheaths, deterioration of rubber used at joints and moving sections is also a major cause of the ingress of cutting oil.
Hence to prevent rubber deterioration, we uniquely develop a new fluorinated rubber used at joins and moving sections. Combined with fluororesin cables, this form an impregnable wall of oil resistance.
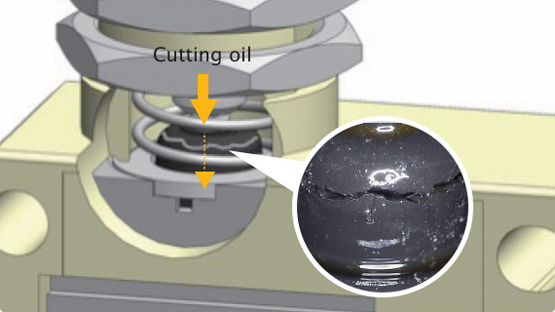
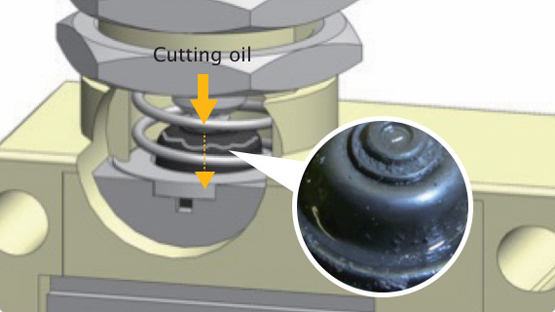
State Of The Art Heat-Sealing Methods
Heat Sealing MethodLaser Welding Method
Ingress Through Cable Joints Is Blocked with OMRON Heat Sealing and Laser Welding Methods
In addition to cable sheaths, joints, and moving sections, cutting oil also enters easily in the gaps of different materials.
With OMRON Advanced Sealing Methods,the Heat-Sealing Method and the Laser Welding Method (for complete sealing without Adhesive), it allows completing sealing of joints of both metal and non metal parts, thus blocking the ingress of cutting oil by preventing the creation of gaps.
A. Heating Seal Method
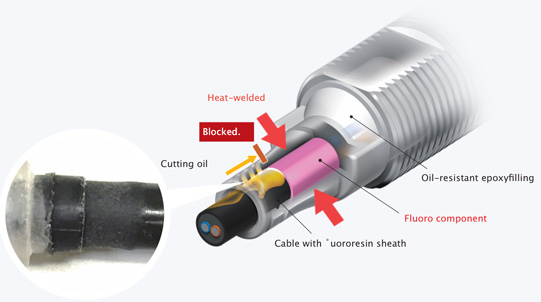
B. Laser Welding Method
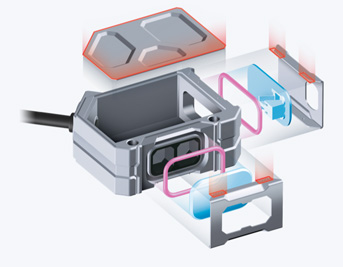
Unique Smartclick Structure
Smartclick Structure + O-ring

Overcome oil-ingress gaps created due to screw tightening or screw losing due to vibration
With traditional screw-tightened structures, differences in tightening torque made achieving oil resistance difficult. OMRON’s Smartclick structure, however locks in a single operation.
The built-in O-ring at the lock position is dependably compressed to block the ingress of cutting oil. This eliminates the need to manage screw tightening torque and prevents screw loosening due to vibration, which are issues in environments requiring oil resistance.
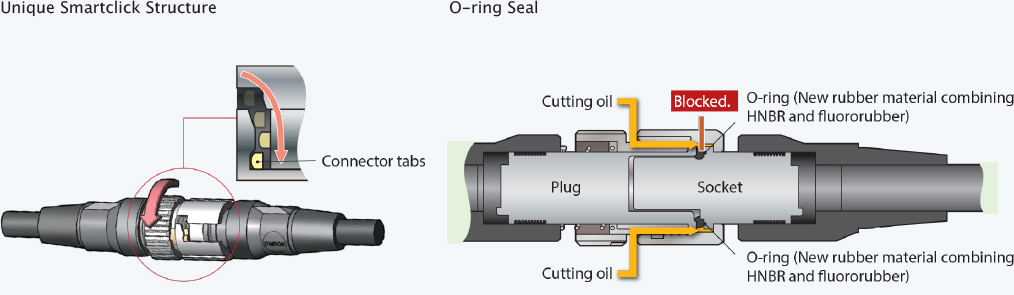