Zero Spillage
Current Issue
Contamination Risk & Wastage
Due To Product Spillage
Costs increase when products are wasted in production runs. By increasing machine speed for liquid transfer, it can often lead to spillage and unnecessary product wastage. When hygiene in the production floor is not managed well (e.g. spillage remains during recipe changeovers), contamination may occur.
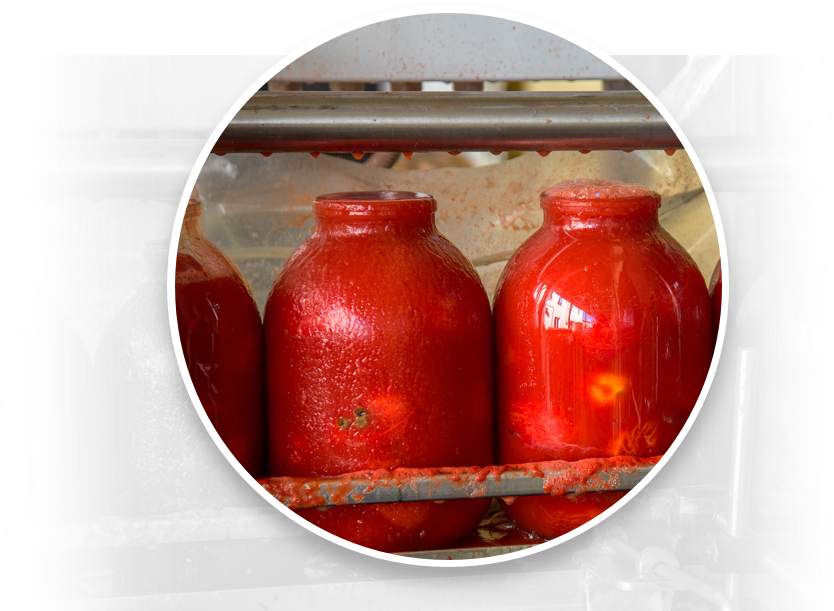
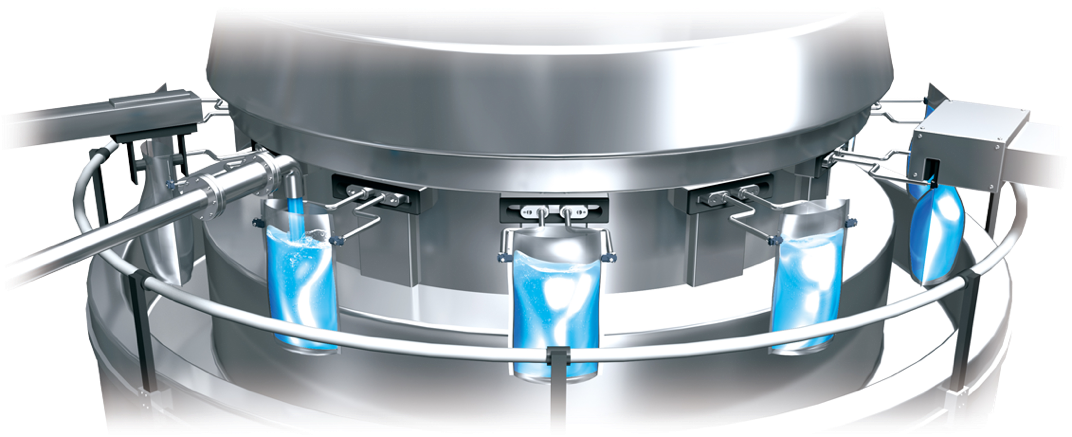
Business Value
Minimize Wastage & Contamination Risk
With Zero Spillage
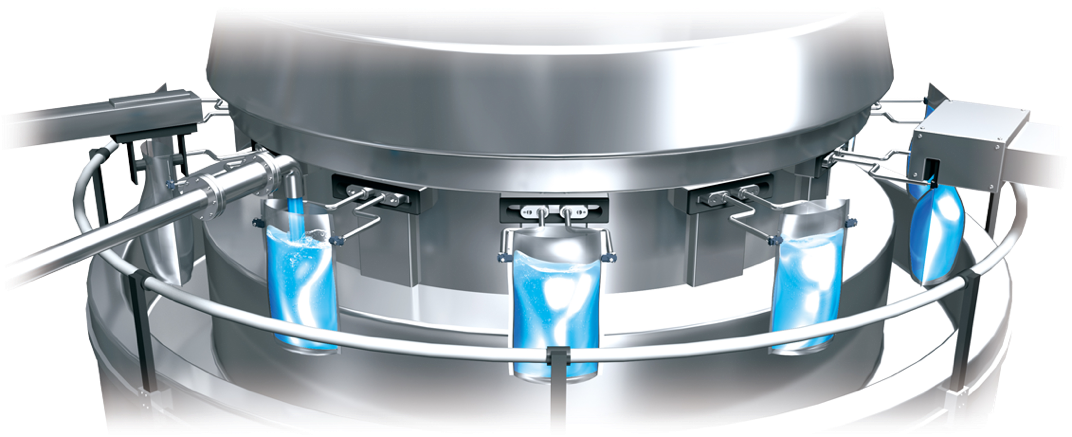
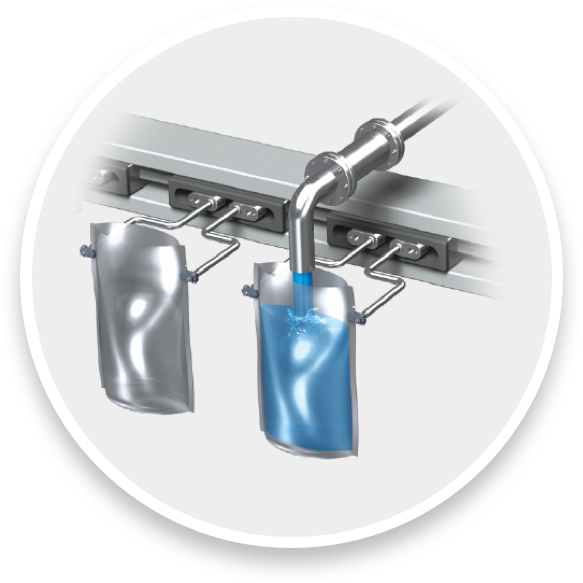
It is absolutely necessary to have a reliable solution to maximise line throughput, while minimizing wastage and food contamination issues that may arise. With OMRON Vibration Suppression Technology that keeps sloshing to a minimum when the machine runs at faster speed, zero spillage is now possible.
Watch how it worksOur Technology
Vibration Suppression with OMRON 1S Servo & NJ Controller
Sloshing
suppression |
Spilling
suppression |
|
---|---|---|
Without VS |
![]() |
![]() |
With servo driver![]() |
![]() |
![]() |
With VS in
Sysmac Machine Automation Controller ![]() |
![]() |
![]() |
In conventional handling without any vibration suppression technology, sloshing can cause liquids to spill over. This negatively affects filling, sealing and measuring processes that slow down production line.
Independent servo driver may be employed to reduce sloshing to a certain degree. This means less space is required to account for sloshing. Therefore, container height can be lowered, reducing the amount and cost of packaging materials.
In order to maximise throughput* and eliminate spillage, we have an easy solution for you. Introducing OMRON anti-slosh technology, it shortens the wait time needed for the packaging contents to settle. OEMs and manufacturers can now achieve faster filling and sealing rates, as well as faster production cycles.
*Packaging lines that implement anti-slosh motion control typically sees an improvement in the throughput from 10% to 50%.