With an IO-Link Photoelectric Sensor
A light incident level monitorprevents false detection
How It Works
With a response time of 1ms, the IO-Link Photoelectric Sensor is able to monitor the light incident level.
Predictive Maintenance To Prevent False Detection
When the light incident level exceeds the instability detection threshold, the maintenance engineer will receive the notification on his display, and perform predictive maintenance before false detection occurs.
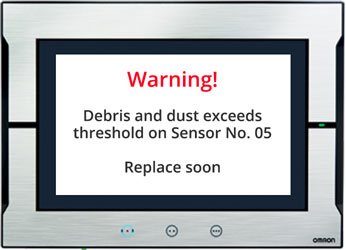
