Securing Connectivity from Operational Technology to it
Early Detection and Error-Proofing
Production chain disruptions can occur in the process of converting silicon wafers into semiconductor chips. This results in serious chip defects. However, it is almost impossible to determine the source of the defect due to the numerous resources and steps involved in this process.
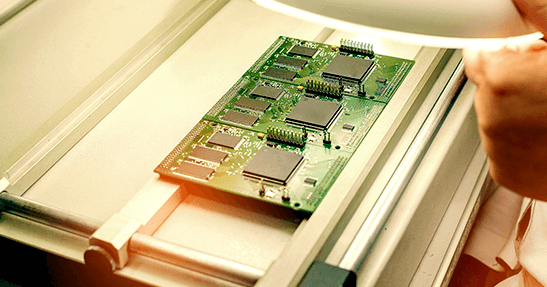
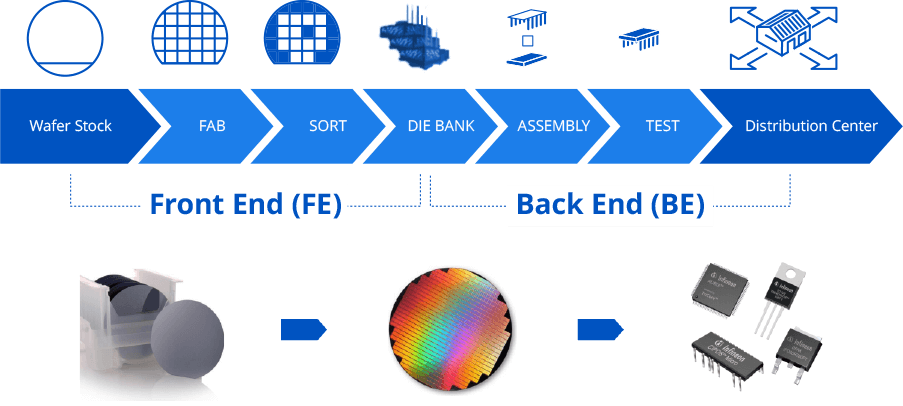
The semiconductor manufacturing industry requires high-speed provisioning of chips with traceability and anti-counterfeiting for early detection of faulty chips as well as to pinpoint chips required for remanufacturing. The more automated a traceability system is with real-time decision tracking, the better it is at analysing the production process and rooting out problem steps.
Using wrong materials (batch or part number) to build parts, will have a damaging impact on the business. Lost production time and wasted materials cause shipment delays which results in customer dissatisfaction. This time-consuming process not only increases waste, it increases cost.
Codes (Direct Part Marks, 2D Codes) need to stay readable for extensive periods of time through the harshness of manufacturing processes. Verifying quality codes are imperative before the parts are shipped from the factory. At the packaging stage, an intelligent raster laser is capable to capture and read multiple code types from a distance.
Integration of OT and IT
Omron Traceability Solutions collect data from Operational Technologies (OT) and interfaces it with Information Technology (IT). Integrating the industrial OT to IT is the IOT challenge. Industrial networks like Ethernet/IP, Ethercat, Profinet may require long hours spent integrating and converting protocol that will connect the interface to an ERP/MES system.
Omron offers comprehensive solutions to eliminate conversion. The multiple secured connections ensure data is safe. This speed up in data connectivity, reduces time and human errors.
Why Omron?
Omron Traceability Solutions reduces the risk of errors. This is crucial especially when electronics manufacturing, and semiconductor industries are making microchips even smaller. The lack of surface area means barcodes for tracking need to be reduced in size but remain readable. Omron uses high resolution 2D or dot size barcodes that store more information and can be read from a distance.
At every stage of interim production, the material, process and test information, can be stored in Radio Frequency Identification (RFID) tags, when Ethernet network connectivity is not available. An automated error proofing check can be used to track and collect production updates in real-time and consistently verify the data collected along the entire supply chain. Furthermore, Omron’s code readers that have colour options are essential to read the data and check for errors.
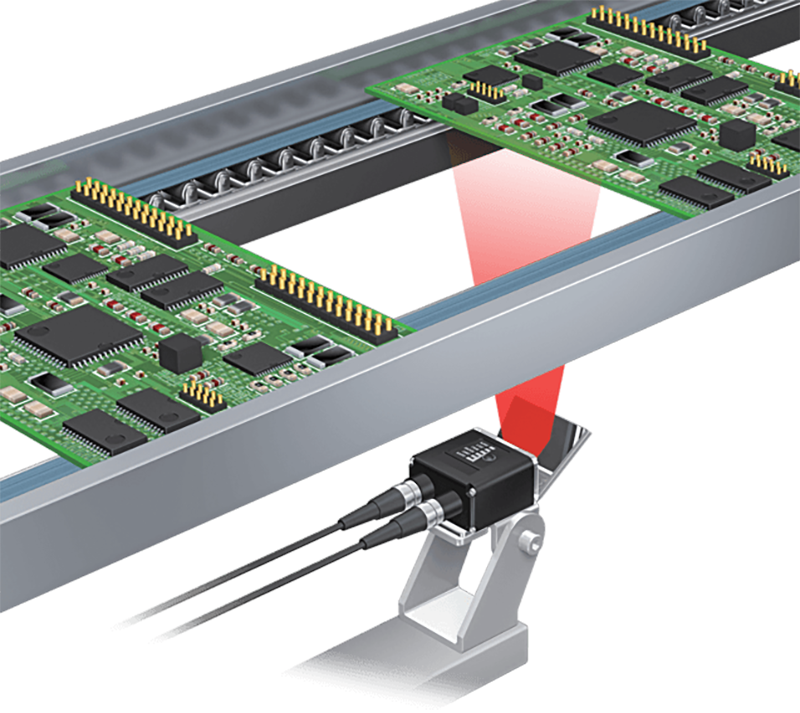
Omron offers one-stop solutions to implement a robust traceability system for Digital Electronics Industry.
productsDownload OMRON Traceability Whitepaper for Digital Electronics Industry Now!
download whitepaper contact us