Build A Vision-Guided Robot In 5 Steps
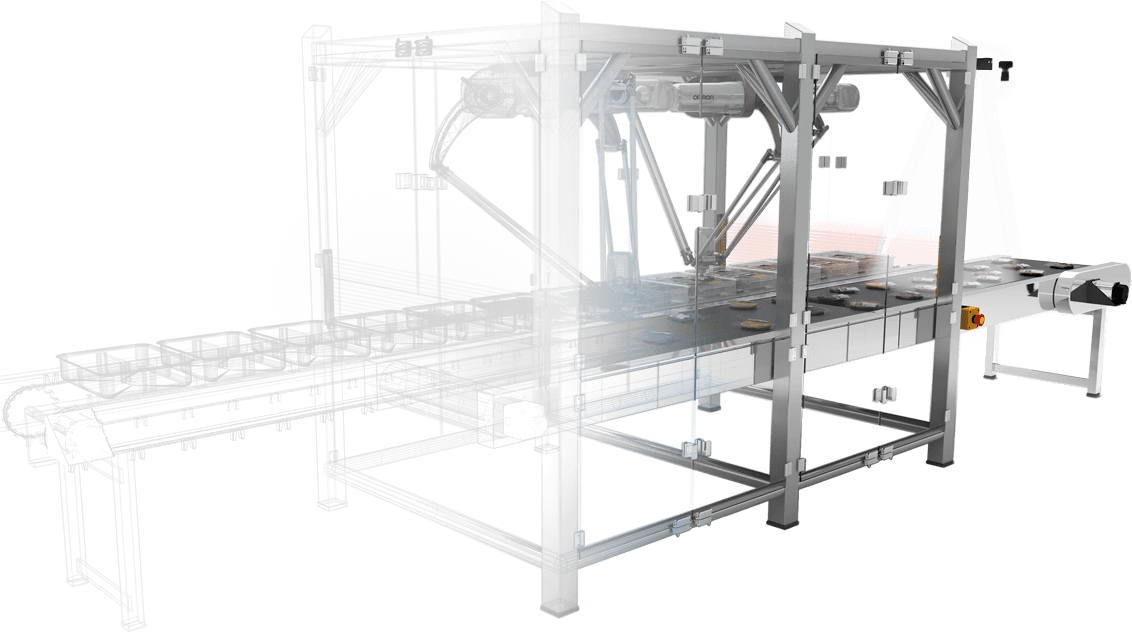
Far from the old and rigid top-down programming manner, our solution is based on Wizards that guide the user through the main steps using a graphical interface to operate with an unique software tool capable to manage Robotics and Vision seamlessly at the same time.
Achieve Time Optimization And Reduction For Your Project
Programming and managing an entire chain of robots have never been easier
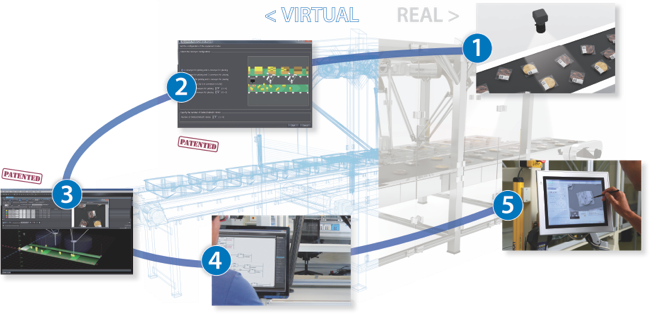
Using clever software tools and Wizards, we allow the user to break away from the old and rigid top-down programming manner of old. Through visualisation and simulation of your packaging line before building or modifying the entire robotic line, you get to achieve cost savings, and a reduction in time for project completion.
Our intuitive design and simulation software gives you greater flexibility to take advantage of the integrated system. By leveraging performance data from a single source, you could increase productivity and efficiency.

Image Capturing
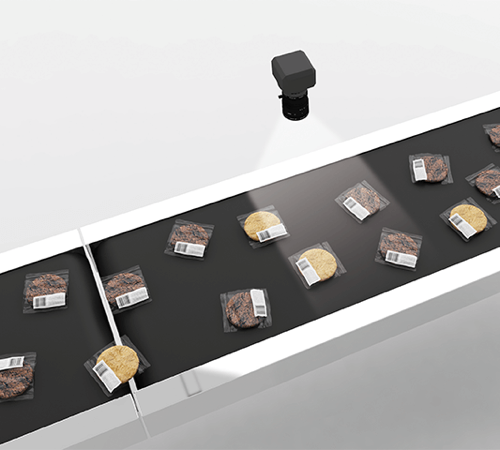
- The first step is to take the pictures of the products to handle. Yes just as easy as it sounds!
- The wide portfolio of our FH cameras allows to optimize your choice.
Import The Pictures Into Sysmac Studio Wizard
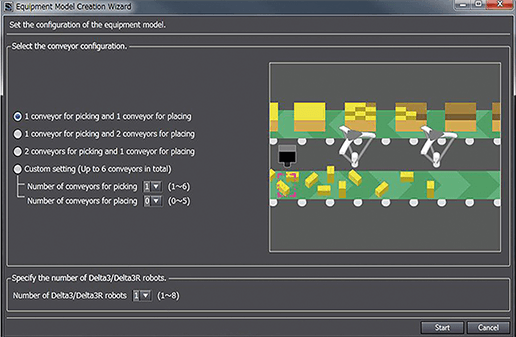
3D Simulation
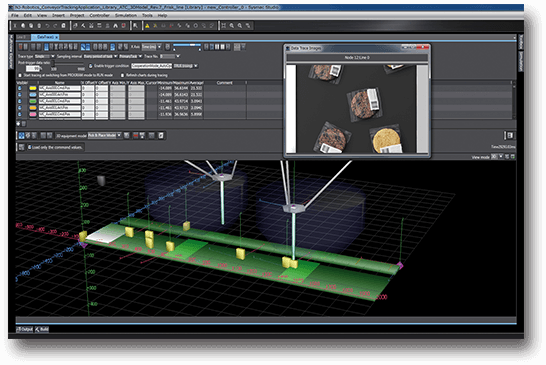
- Sysmac Studio generates the 3D simulation environment according to the parameters defined in the previous steps.
- The integrated graphical environment enables visualizing the Pick & Place machine and the Vision simulation at the same time.
- Moreover, the images captured in the Step 1 are automatically converted into the corresponding virtual products that run over the picking conveyor.